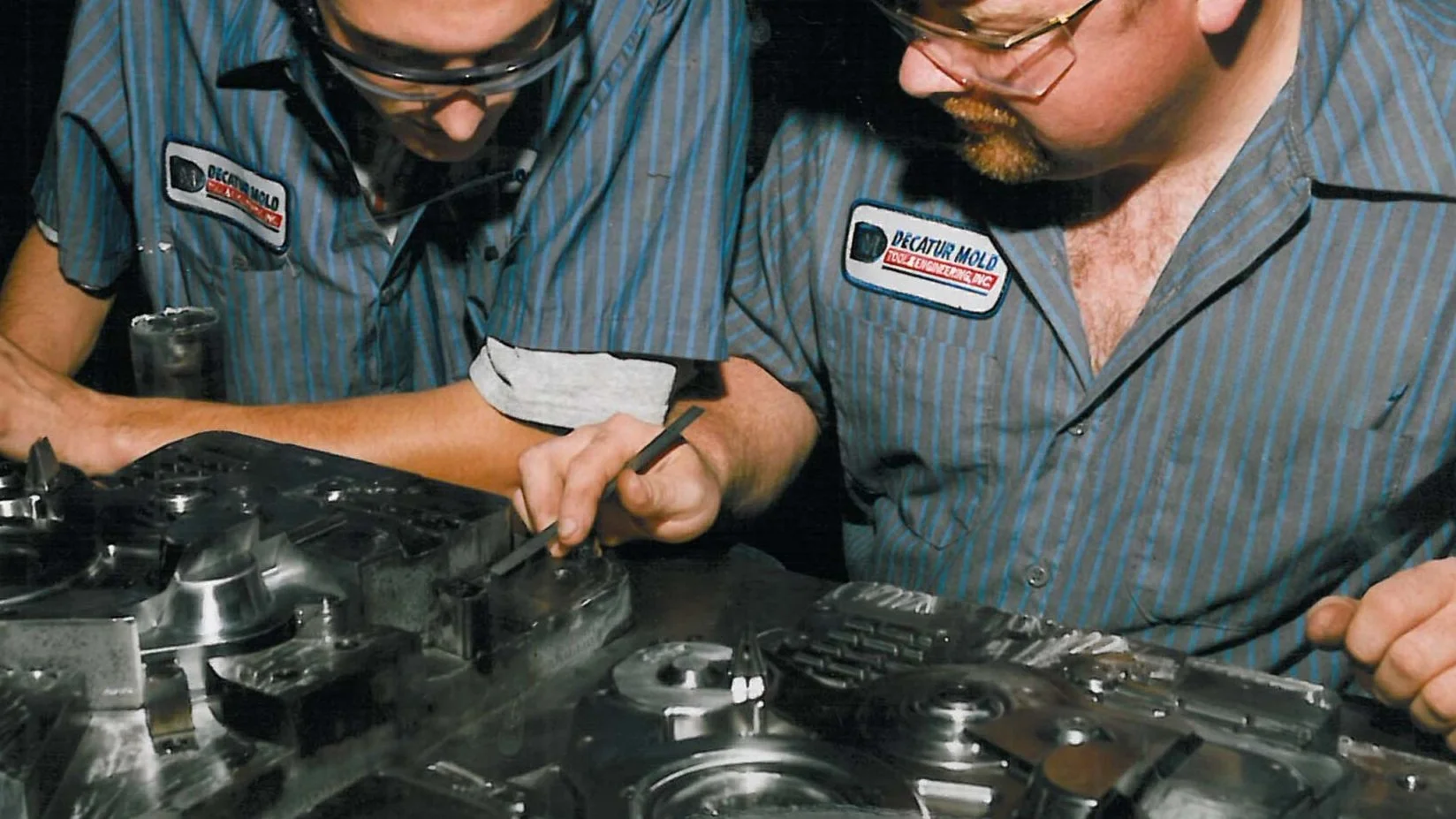
Tooling Experts: Reducing Uncertainty, Lightening Workloads
Experience the Difference.
There are no “tools” on our team, only experienced crafters and specialists. With over 50 years of experience, Decatur Mold Tool & Engineering, Inc. has established itself as a leader in the injection mold and tooling industry. Our expert team utilizes advanced CAD design and state-of-the-art CNC machining to create high-quality, precision-engineered molds and tools. We are committed to innovation and excellence, ensuring that every project meets the highest standards of quality and accuracy.
Flexibility
Precision Results
Efficient Processes
High-Quality Tooling & Injection Molding Services
-
Production Molds
-
Prototype Molds
-
Mold Repair and engineering changes
-
Design and Reverse Engineering
-
Custom Machining
-
Sampling and Low Volume Molding
What’S New at DMTE?
While our new Technology Center has increased capacity and productivity, we have maintained a strong focus on quality as well. We've made improvements in programming, tool setting, and machine accuracy. All our technological advancements result in tools produced precisely according to specifications, requiring little to no rework. Tools made true to data allow our customers to have confidence, knowing that future engineering changes or repairs can be completed seamlessly.
Revitalizing Tradition: dECATUR mOLD’s Innovative Path
Your Tooling Tour Guides. Connect with Our Sales Team Today
-
Kenneth Overfelt
Decatur Mold Sales
-
Steve Schmidt
Decatur Mold Sales
-
Bert Shaw
Decatur Mold Sales
-
Baron Wilder
Decatur Mold Sales
Equipped to meet all your tooling needs.
-
CNC Machines
EDM Robotic Cells
Electrical Discharge Machines
Turning Equipment
Handling Equipment
Drilling Equipment
Spotting Equipment
Milling Machines
Grinding Equipment
Inspection Equipment
Welding Equipment
Delivery Trucks
Injection Molding Machines